Digital Transformations Kirin Group's Digital Strategy
Message from the Executive Officer
To deliver optimal value to every customer
KIRIN Digital Vision 2035 was formulated to accelerate the digital transformation of the Kirin Group, which aims to become a global leader of CSV.The Kirin Group prioritizes every employee to identify social issues and take on the challenge of solving them.We want employees to think of customers first and try to realize their own ideas by making full use of digital technologies.For example, aiming to provide personalized and longstanding services for every customer by utilizing Kirin's unique customer data and AI-powered customized services is a possibility.We have already started POC in some areas and are moving towards becoming a leading CSV company that the Kirin Group aims for.In order to devote time to creating value for customers and society, we aim to increase productivity using AI, which results in relying on the technologies to do tasks that do not require human intervention.Through these initiatives, we aim to create an exciting future.By making the most of every employee’s creativity to provide new value to society, our company will continue to evolve.We are truly looking forward to building a better future together with you.
Mitsuharu Yamagata Senior Executive Officer
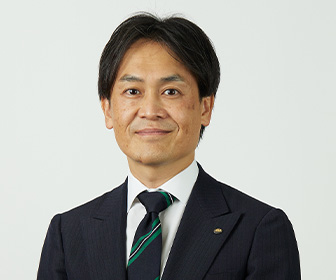
KIRIN Digital Vision 2035
Our goals through Kirin's DX (Digital Transformation)
Under Digital Vision 2035, we aim to become a leading CSV company globally by enhancing the digital infrastructure that supports “productivity improvement” and “value creation,” the two pillars of our business goals. Thereby we will dramatically improve the quality, quantity, and speed of value creation in food, health science, and medicine.
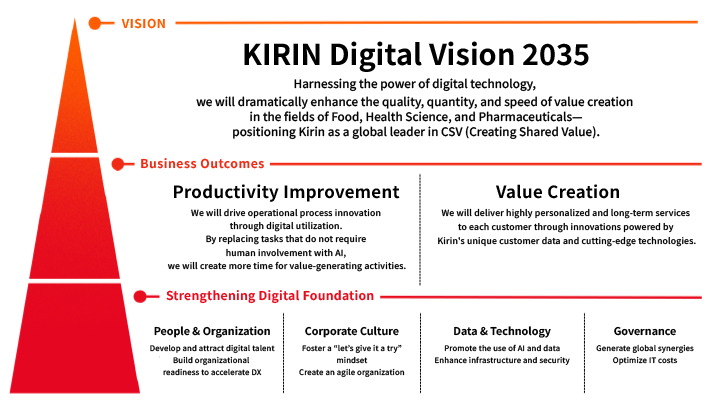